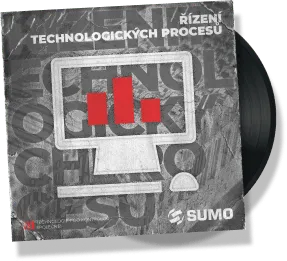
Management of technological processes
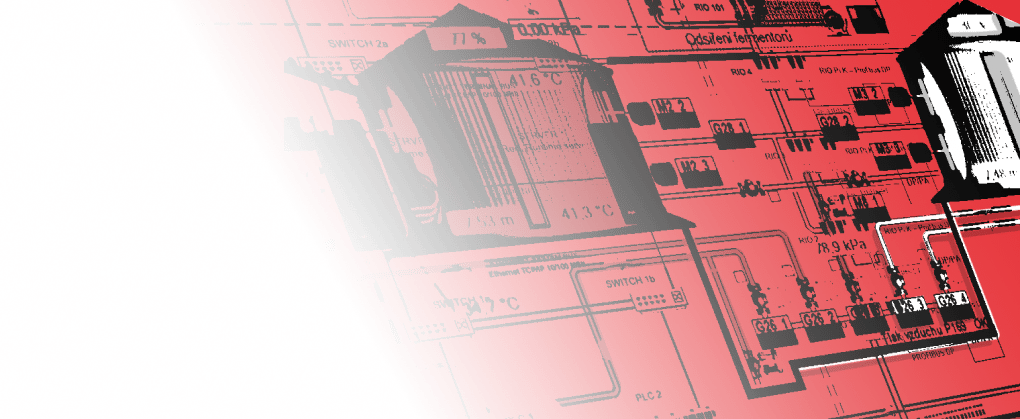
WE OPTIMISE YOUR PRODUCTION AND REDUCE PRODUCTION COSTS
Advanced control systems implemented in modern operations ensure that you are always in control of production, reducing your production costs. For the implementation of complete orders, we have an experienced team of specialists who have many years of experience in the field and work with the most advanced equipment.
After completing the order, you have the option of using our 24/7 Service, which will help you avoid unexpected downtime in production.
We will increase your production efficiency
We implement complex PLC/DCS control systems
We use modern tools and equipment
We can monitor technology remotely
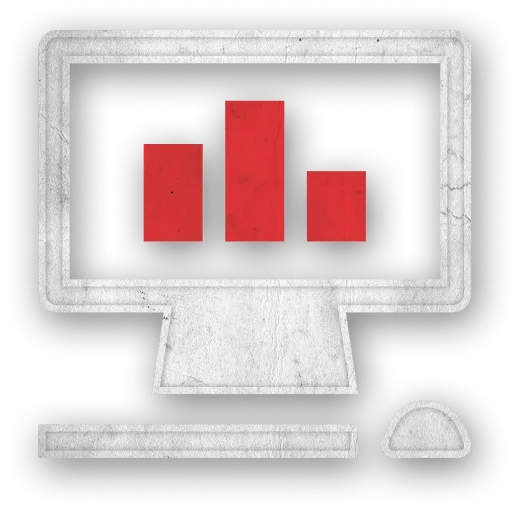
We automate your production processes
Based on the functional description of the technology, we will create algorithms with which we will program software for control systems (PLC/DCS). In order for the technology to be controlled by the operator, we will prepare a visualisation for the operator's workplace (SCADA/HMI).
As we have our own production of distribution boards, we can test the system (FAT) before it reaches the customer. Thanks to this, we reduce the commissioning time to a minimum.
The code also includes monitoring of the operational status of the equipment, which is used to predict the failure of machines and systems even before they occur.
what we can do
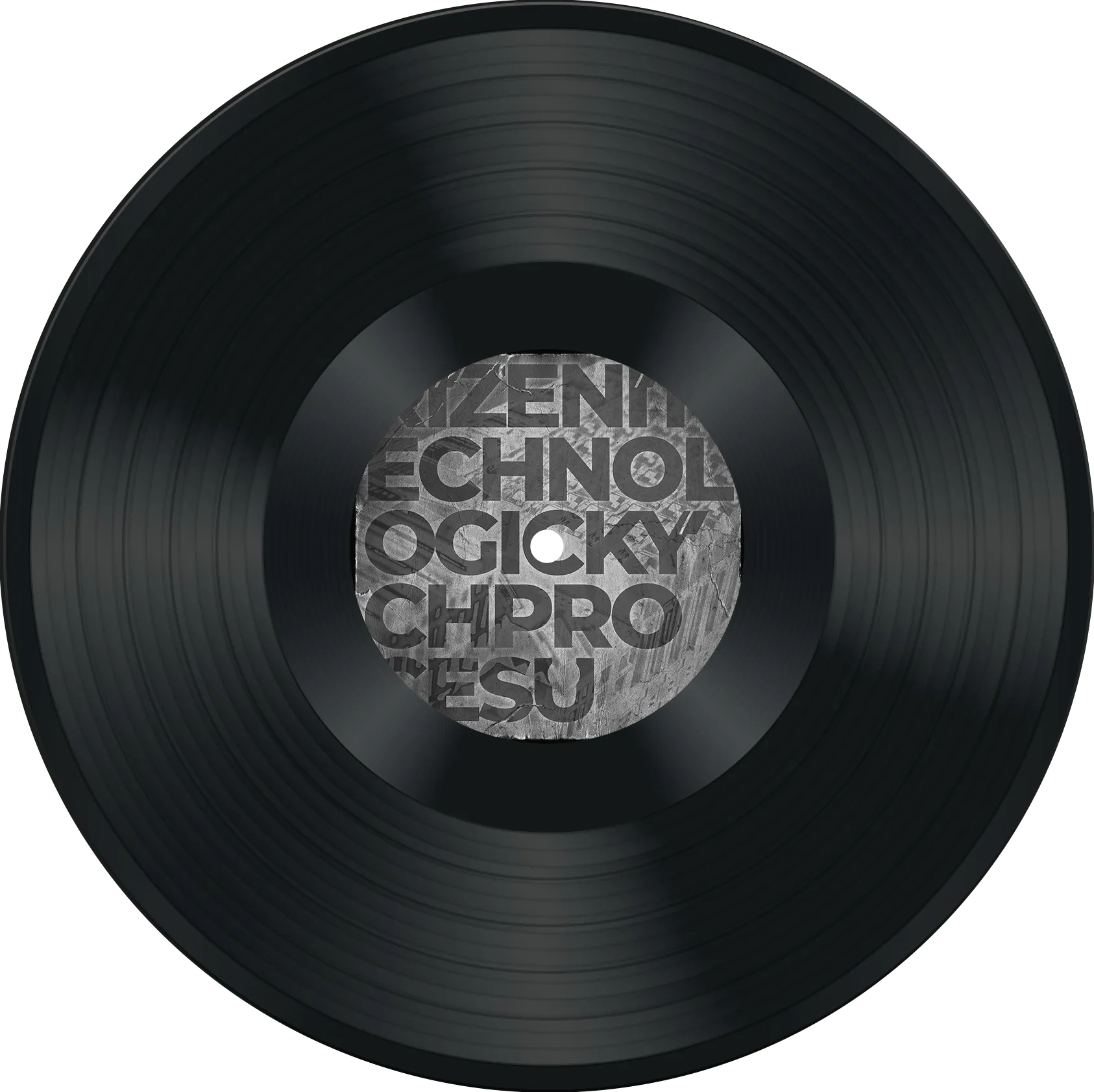
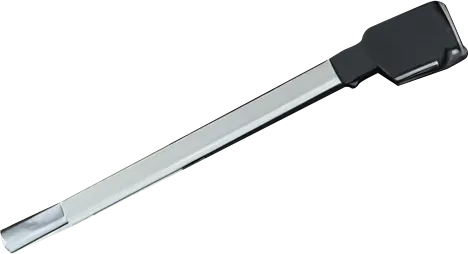
Draft solution and design
First of all, we get to know your manufacturing process and thoroughly analyze your individual operations. Based on the analysis, we will suggest optimization options. We emphasis on high quality and useful value of the entire system. When designing the control system, we use many years of system and technological experience. At the same time, we only use verified components from brand manufacturers Siemens, Rockwell, B&R, TECO, Mitsubishi, KOYO, AMiT and others.
For demanding applications with a high number of I/O signals and extensive dispatching workplaces, we equip complex PLC/DCS with control systems.
We create visualisations for operator stations on PCs (Reliance, WinCC, RS View, FT View, Citect) and touch panels (Siemens, Weintek, B&R, Rockwell) to monitor current and historical operational and fault conditions.
We use Profibus DP/PA, Profinet, Modbus (RTU, TCP/IP), MBus, SNMP, EtherNet/IP, HART, ASCII protocols for communication.
Activation of technology
Part of putting the equipment into operation consists in individual tests (IZ), where individual parts of the system are checked. The next stage is the pre-comprehensive testing (PKV), where we check the supplied system with the medium in coordination with the tests of other suppliers. As part of the pre-comprehensive tests, training and familiarisation of workers are taking place. The conclusion is a comprehensive test (KV), which is used to prove the designed properties of the delivery, mostly with 72-hour continuous operation and compliance with the nominal parameters.
Predictive service maintenance
The advantages of technological process management include the prediction of machine failures due to their wear and tear. We simply detect wear and tear before the device malfunctions and stops. Advanced measurement and control systems collect information that is evaluated by the control system. Both for the needs of production management and for reporting on the frequency of performed operations or operating hours. Furthermore, vibrations, temperatures, operating pressures and other quantities are evaluated. Thanks to this, we detect stressed components and replace them before they fail. By maintaining electrical equipment, we prevent unplanned production shutdowns and enable efficient planning of service interventions, which reduce the financial costs of production shutdowns.
In real time, we collect and evaluate data on the utilisation of production components.
We evaluate vibrations, operating temperatures, pressures and other quantities.
We prevent unplanned production shutdowns.
We reduce maintenance costs.
Industry 4.0
The advantages of technological process management include the prediction of machine failures due to their wear and tear. We simply detect wear and tear before the device malfunctions and stops. Advanced instrumentation and control systems collect information that is evaluated by the control system. Both for the needs of production management and for reporting on the frequency of performed operations or operating hours. Furthermore, vibrations, temperatures, operating pressures and other quantities are evaluated. Thanks to this, we detect stressed components and replace them before they fail. By maintaining electrical equipment, we prevent unplanned production shutdowns and enable efficient planning of service interventions, which reduce the financial costs of production shutdowns.
Upgrade řídících systémů
V rámci servisu a realizace investičních akcí dále nabízíme zákazníkům upgrady zastaralých řídících systémů. Systémy, které již nemají na trhu dostupné náhradní díly a od výrobců skončila veškerá podpora, nahrazujeme novými systémy Siemens, Allen Bradley nebo B+R Automation. Vše zajistíme „na klíč“ včetně projektové dokumentace, úpravy rozvaděčů a aplikačního SW. Vše probíhá tak, aby vaše technologie byla co nejkratší dobu odstavená.
When we succeed, we like to brag
We have successfully implemented over 6,000 projects in the energy sector, chemical industry, water management and other industries.
I want automation
In the report, specify your request in as much detail as possible so that we can help you in the best possible way.